機械システム安全研究グループ 材料試験機および電子顕微鏡による破断面観察の紹介
機械システム安全研究グループでは、機械・設備に起因する労働災害の防止を目的として、機械等の構造部材の強度評価、部材の破断面観察による破損要因の解明、自動化機械等のフェールセーフ技術の開発、リスクアセスメントに基づく安全設計手法の開発などに関する研究を行っています。この中で、機械等の構造部材の強度評価および部材の破断面観察による破損要因の解明は、製造現場や建設現場で使用される多種多様な機械の破損防止や災害原因の究明に役立ちます。ここでは、構造部材の強度評価および破断面観察を行う際に使用される試験装置を紹介いたします。
製造現場や建設現場では多種多様な機械が使用されています。機械の多くは高度経済成長期に製造されたものも多く、そのような機械は設計寿命を大幅に超えて使用されています。設計寿命を超えて使用される機械の構造部材は、疲労破壊という破損をしばしば起こします。疲労破壊は一定の荷重を繰返し受ける場合や荷重が不規則に変動する場合に生じます。この疲労破壊を防止するためには、構造部材の強度評価をおこない、その部材の疲労特性(繰返しの力を与える試験(疲労試験)によって得られる部材の性質)を知る必要があります。そこで、構造部材の疲労特性を得るために、構造部材を模擬した試験片を作成して、図1に示すような電気油圧サーボ型疲労試験機に試験片を取り付け、繰返しの荷重を作用させることで、部材の疲労特性を実験的に得ます。図中の試験機は最大荷重容量が500 kN(50トンの力)の電気油圧サーボ型疲労試験機です。
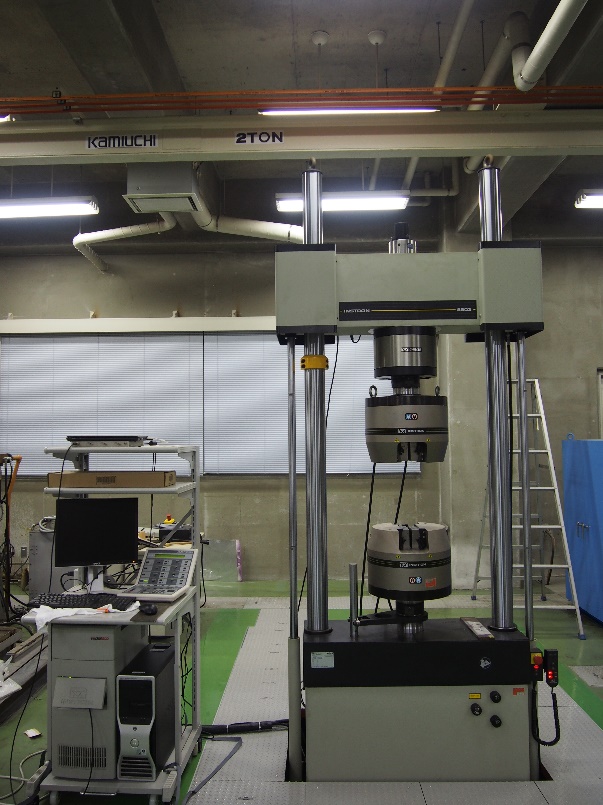
図1 電気油圧サーボ型疲労試験機(最大荷重容量:500 kN)
図2に材料試験機が設置されている実験室の一部を示します。機械システム安全研究グループが使用している材料試験機は、電気油圧サーボ型疲労試験機8台、回転曲げ疲労試験機3台、超音波疲労試験機1台、ロープ疲労試験機1台であり、部材の形状や大きさ、試験方法などに応じて、使用する材料試験機を選択しています。たとえば、曲げの荷重を常に受けるような細長い部材に対して、曲げの繰返し荷重を与える場合には、図3に示すような基礎を有する材料試験機を使用します。最も大きい荷重容量を有する試験機では1500 kNの荷重(150トンの力)を出力することが可能であり、実際の機械に使用されている構造部材を対象に強度評価を行って疲労特性を得ています。
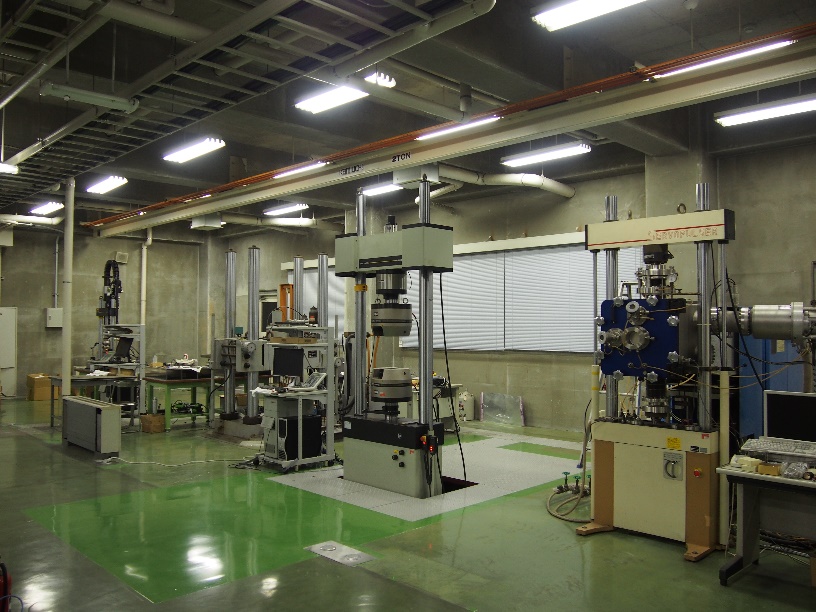
図2 実験室の様子
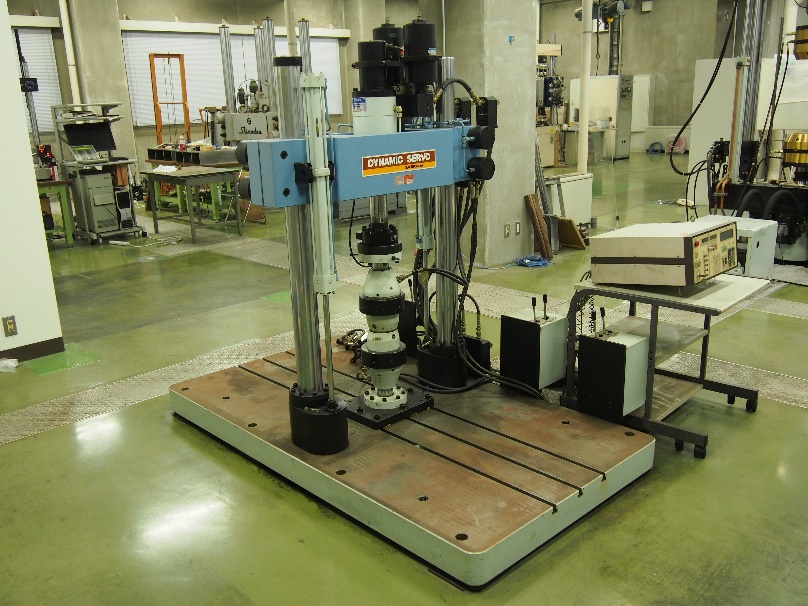
図3 電気油圧サーボ型疲労試験機(最大荷重容量:100 kN)
これまで疲労特性は、荷重繰返し数が1千万回までの試験結果から得られていましたが、近年、一部の部材が荷重繰返し数1千万回以上(超寿命領域)で破壊することが明らかとなったこと、また、溶接継手おける疲労特性は、繰返し数が200万回程度までの試験結果から得られていたことから、超寿命領域における疲労特性の解明が求められていました。そこで、機械システム安全研究グループでは、先に紹介した様々な材料試験機を使用して、 機械等に使用される各種鉄鋼材料の長寿命疲労特性や溶接継手の長寿命疲労特性 を明らかにしました。 詳しくは以下をご参照ください。
鉄鋼材料の長寿命疲労特性について
https://www.jniosh.johas.go.jp/publication/doc/srr/SRR-No40-2-1.pdf [PDF]
溶接継手の長寿命疲労特性について
https://www.jniosh.johas.go.jp/publication/doc/srr/SRR-No40-2-2.pdf [PDF]
部材の破断面観察による破損要因の解明は、図4に示す走査型電子顕微鏡(Scanning Electron Microscope: SEM)を使用して行います。SEMは、破損した構造部材の破断面や材料試験機により疲労破壊した試験片の破断面を観察するために用います。SEMの倍率はその性能によって差がありますが、機械システム安全研究グループが使用しているSEMの倍率は40-600,000倍です。また、SEMはエネルギー分散型X線分析装置(Energy Dispersive X-ray Spectroscopy: EDS)を搭載しており、部材の含有元素や元素分布、その組成比を評価することが可能であり、構造部材に使用されていた金属が適正なものであったか調査することが可能です。
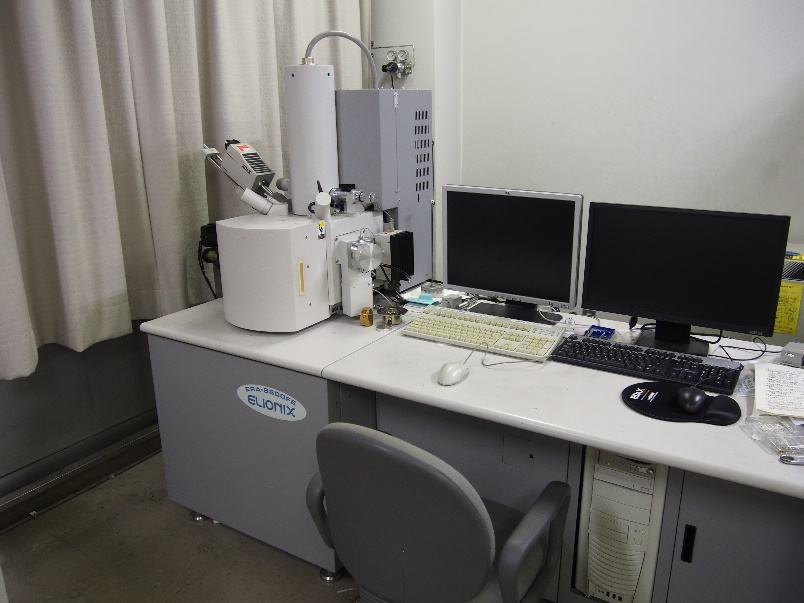
図4 走査型電子顕微鏡の概観
SEMによって部材の破断面を観察すると、図5に示すような、過大な荷重によって部材が変形して破損したときの破断面で観察される(a)延性破壊の破断面や、部材が脆くなって破損したときの破断面で観察される(b)脆性破壊の破断面、繰返しの荷重によって部材が破損したときの破断面で観察される(c)疲労破壊の破断面など、破断面の様相を得ることができます。通常目視では、破断面の差異が分かりにくいため、破損した要因を捕らえることは困難ですが、SEMを用いることで破断面の様相が明らかとなるため、破損要因の解明を行うことが可能になります。
以上のように、機械システム安全研究グループでは、さまざまな材料試験機やSEMをはじめとする顕微鏡を使用して、製造現場や建設現場で使用される多種多様な機械の破損防止や災害原因の究明に努めています。
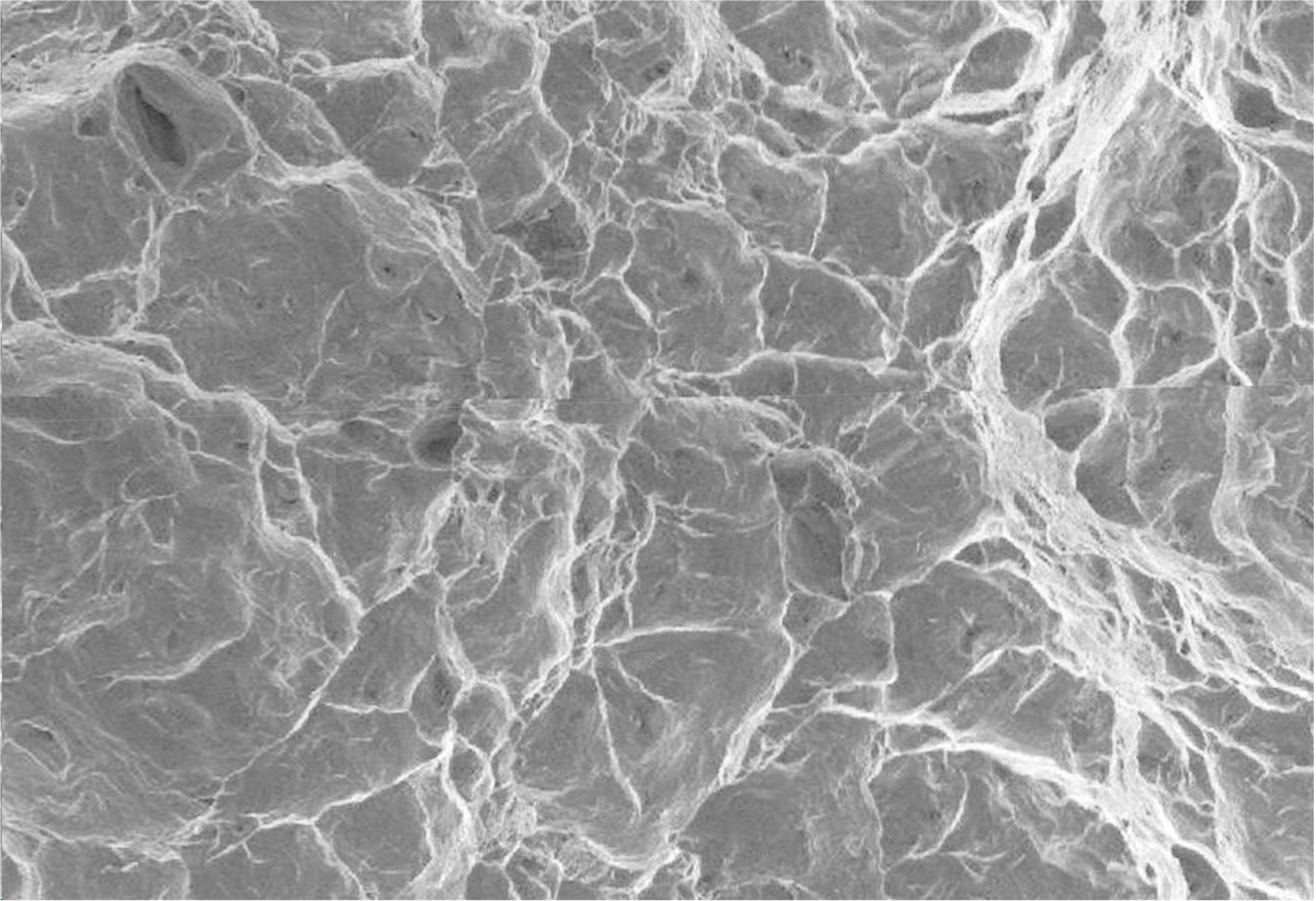
(a) 延性破壊の破断面(ディンプルと呼ばれる小さい穴のような模様が形成される)
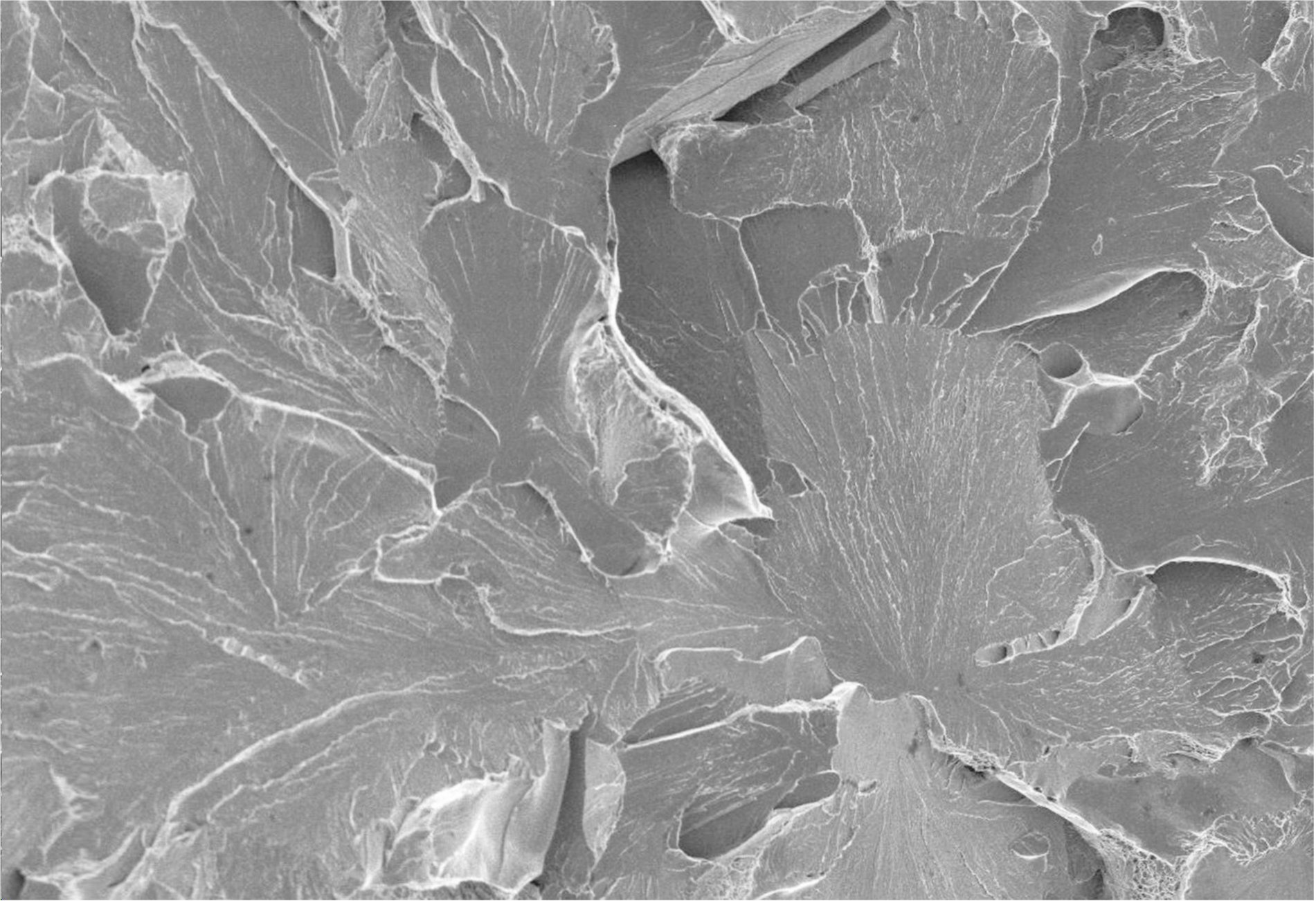
(b) 脆性破壊の破断面(リバーパターンとよばれる川状模様が形成される)
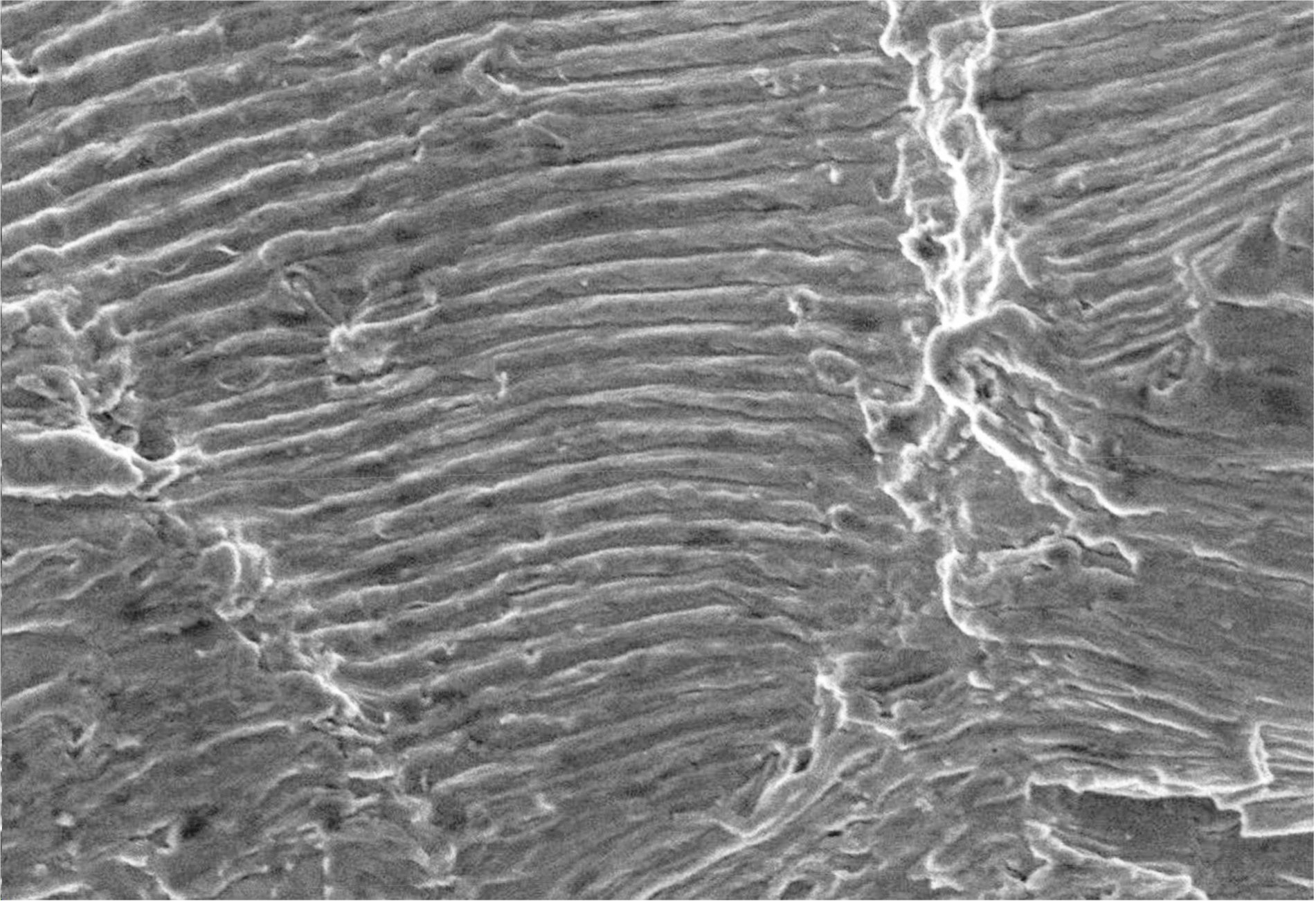
(c) 疲労破壊の破断面(ストライエーション状模様と呼ばれる縞模様が形成される)
図5 走査型電子顕微鏡による破断面の観察結果一例
製造現場や建設現場では多種多様な機械が使用されています。機械の多くは高度経済成長期に製造されたものも多く、そのような機械は設計寿命を大幅に超えて使用されています。設計寿命を超えて使用される機械の構造部材は、疲労破壊という破損をしばしば起こします。疲労破壊は一定の荷重を繰返し受ける場合や荷重が不規則に変動する場合に生じます。この疲労破壊を防止するためには、構造部材の強度評価をおこない、その部材の疲労特性(繰返しの力を与える試験(疲労試験)によって得られる部材の性質)を知る必要があります。そこで、構造部材の疲労特性を得るために、構造部材を模擬した試験片を作成して、図1に示すような電気油圧サーボ型疲労試験機に試験片を取り付け、繰返しの荷重を作用させることで、部材の疲労特性を実験的に得ます。図中の試験機は最大荷重容量が500 kN(50トンの力)の電気油圧サーボ型疲労試験機です。
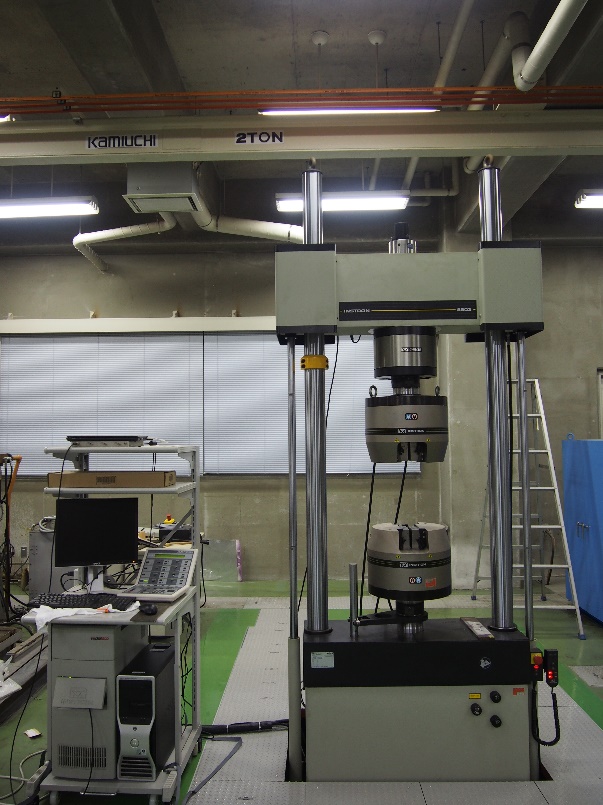
図1 電気油圧サーボ型疲労試験機(最大荷重容量:500 kN)
図2に材料試験機が設置されている実験室の一部を示します。機械システム安全研究グループが使用している材料試験機は、電気油圧サーボ型疲労試験機8台、回転曲げ疲労試験機3台、超音波疲労試験機1台、ロープ疲労試験機1台であり、部材の形状や大きさ、試験方法などに応じて、使用する材料試験機を選択しています。たとえば、曲げの荷重を常に受けるような細長い部材に対して、曲げの繰返し荷重を与える場合には、図3に示すような基礎を有する材料試験機を使用します。最も大きい荷重容量を有する試験機では1500 kNの荷重(150トンの力)を出力することが可能であり、実際の機械に使用されている構造部材を対象に強度評価を行って疲労特性を得ています。
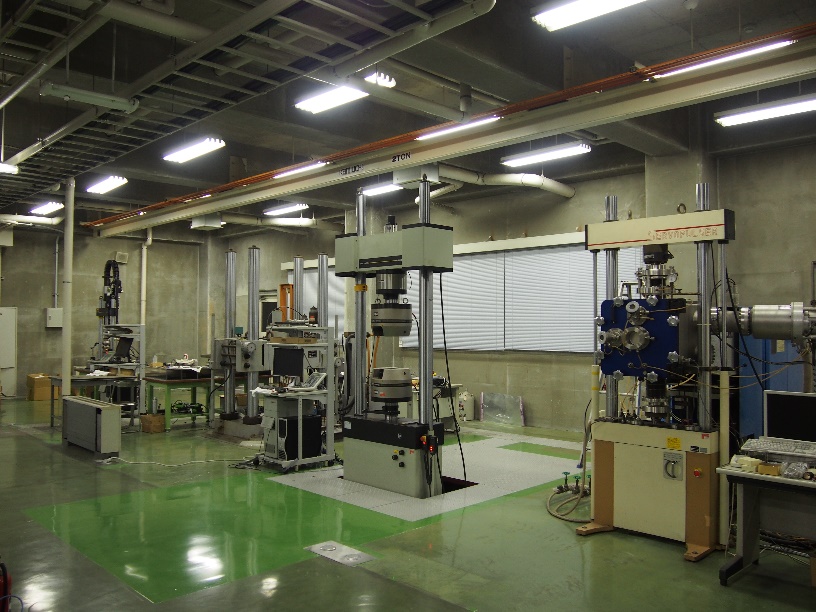
図2 実験室の様子
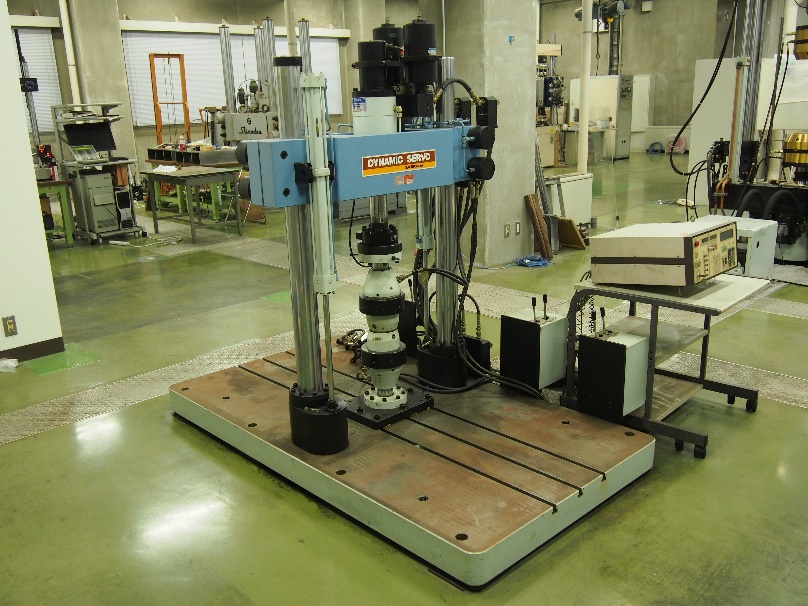
図3 電気油圧サーボ型疲労試験機(最大荷重容量:100 kN)
これまで疲労特性は、荷重繰返し数が1千万回までの試験結果から得られていましたが、近年、一部の部材が荷重繰返し数1千万回以上(超寿命領域)で破壊することが明らかとなったこと、また、溶接継手おける疲労特性は、繰返し数が200万回程度までの試験結果から得られていたことから、超寿命領域における疲労特性の解明が求められていました。そこで、機械システム安全研究グループでは、先に紹介した様々な材料試験機を使用して、 機械等に使用される各種鉄鋼材料の長寿命疲労特性や溶接継手の長寿命疲労特性 を明らかにしました。 詳しくは以下をご参照ください。
鉄鋼材料の長寿命疲労特性について
https://www.jniosh.johas.go.jp/publication/doc/srr/SRR-No40-2-1.pdf [PDF]
溶接継手の長寿命疲労特性について
https://www.jniosh.johas.go.jp/publication/doc/srr/SRR-No40-2-2.pdf [PDF]
部材の破断面観察による破損要因の解明は、図4に示す走査型電子顕微鏡(Scanning Electron Microscope: SEM)を使用して行います。SEMは、破損した構造部材の破断面や材料試験機により疲労破壊した試験片の破断面を観察するために用います。SEMの倍率はその性能によって差がありますが、機械システム安全研究グループが使用しているSEMの倍率は40-600,000倍です。また、SEMはエネルギー分散型X線分析装置(Energy Dispersive X-ray Spectroscopy: EDS)を搭載しており、部材の含有元素や元素分布、その組成比を評価することが可能であり、構造部材に使用されていた金属が適正なものであったか調査することが可能です。
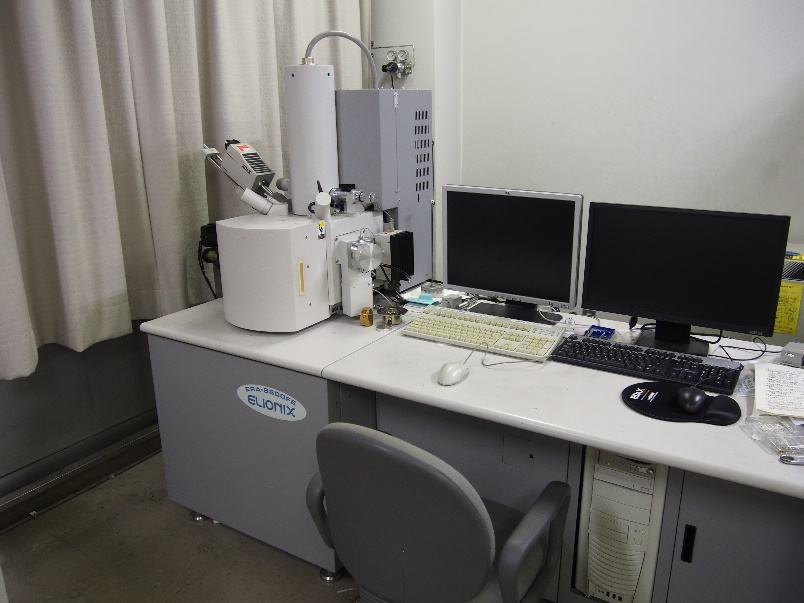
図4 走査型電子顕微鏡の概観
SEMによって部材の破断面を観察すると、図5に示すような、過大な荷重によって部材が変形して破損したときの破断面で観察される(a)延性破壊の破断面や、部材が脆くなって破損したときの破断面で観察される(b)脆性破壊の破断面、繰返しの荷重によって部材が破損したときの破断面で観察される(c)疲労破壊の破断面など、破断面の様相を得ることができます。通常目視では、破断面の差異が分かりにくいため、破損した要因を捕らえることは困難ですが、SEMを用いることで破断面の様相が明らかとなるため、破損要因の解明を行うことが可能になります。
以上のように、機械システム安全研究グループでは、さまざまな材料試験機やSEMをはじめとする顕微鏡を使用して、製造現場や建設現場で使用される多種多様な機械の破損防止や災害原因の究明に努めています。
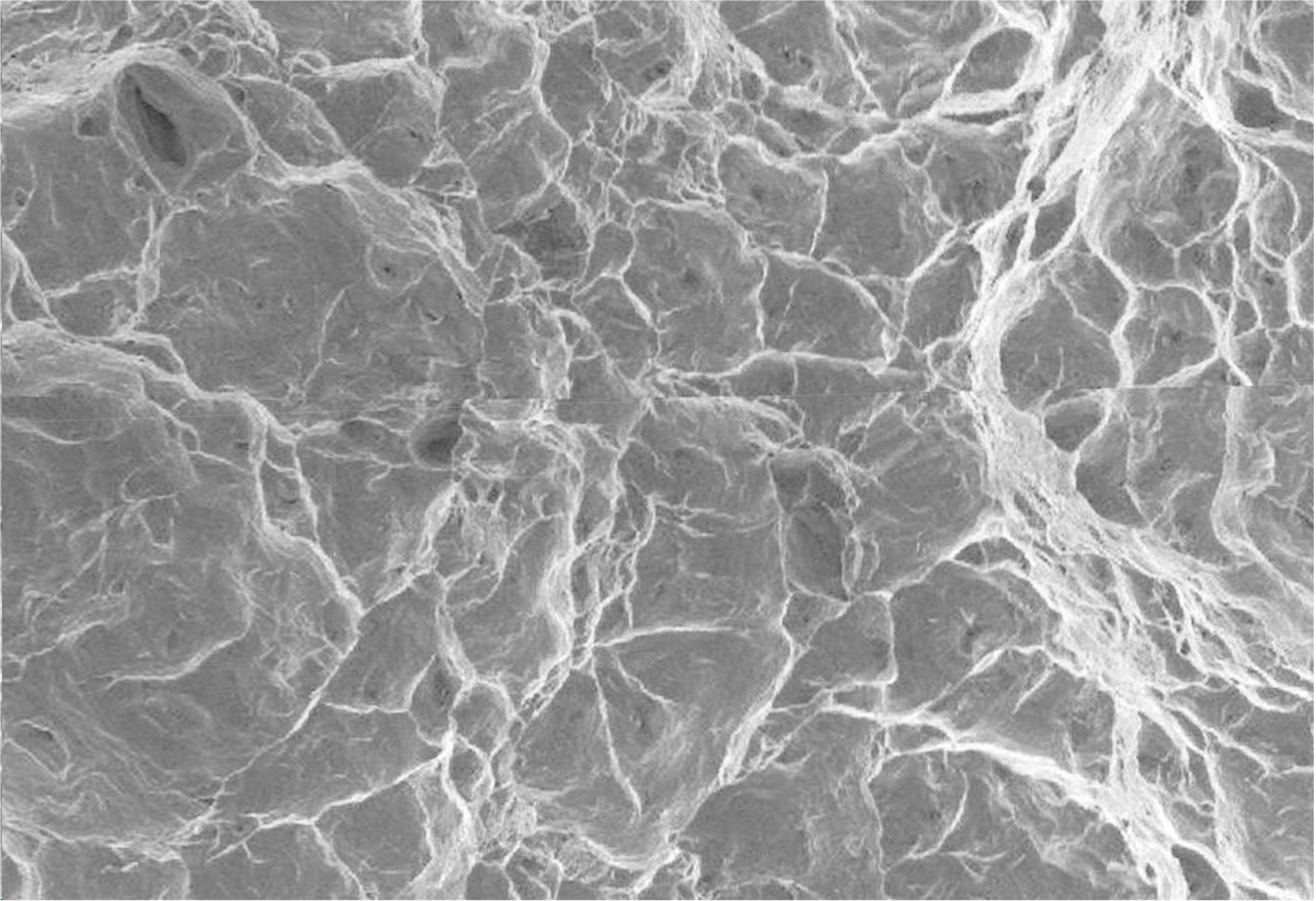
(a) 延性破壊の破断面(ディンプルと呼ばれる小さい穴のような模様が形成される)
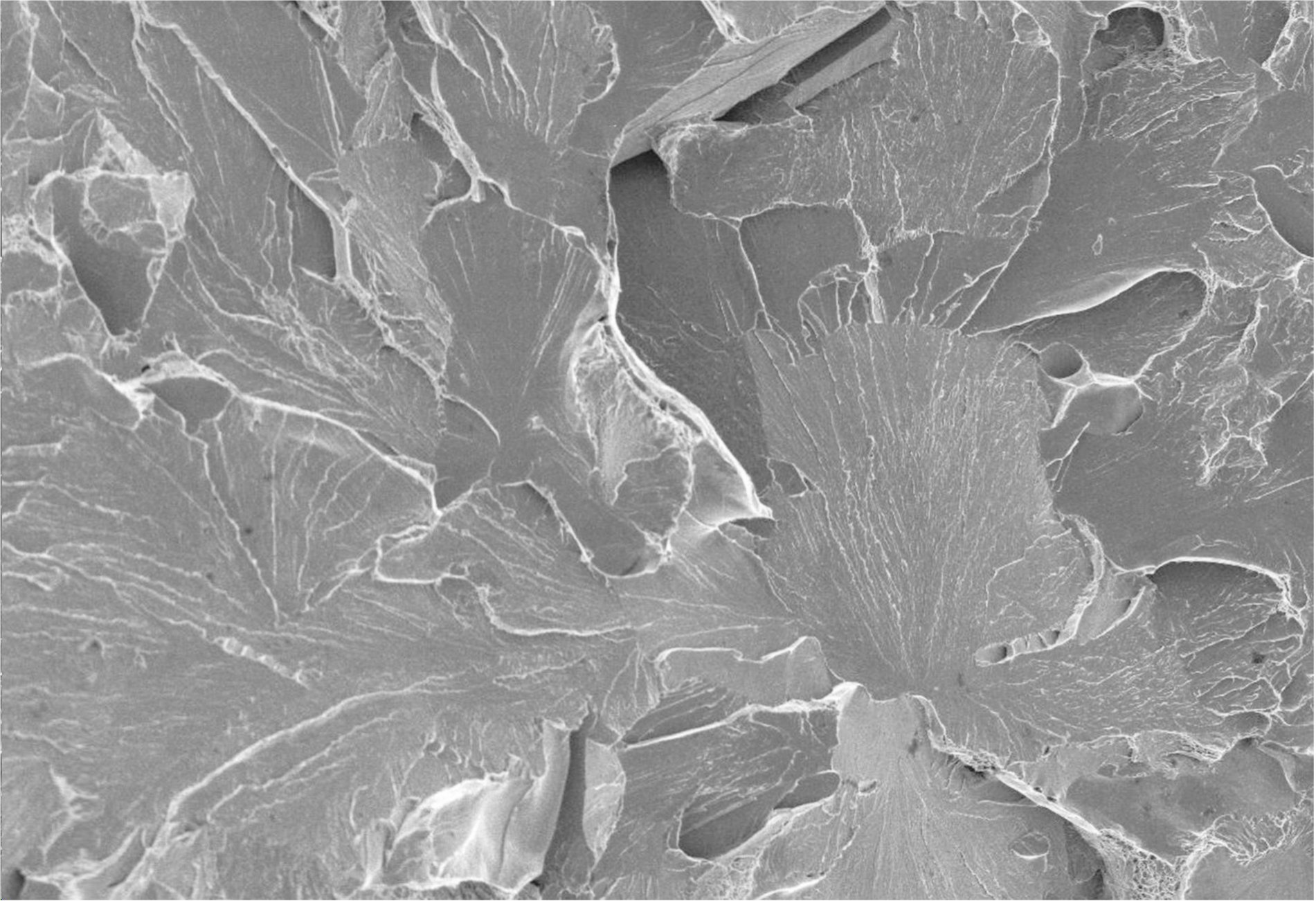
(b) 脆性破壊の破断面(リバーパターンとよばれる川状模様が形成される)
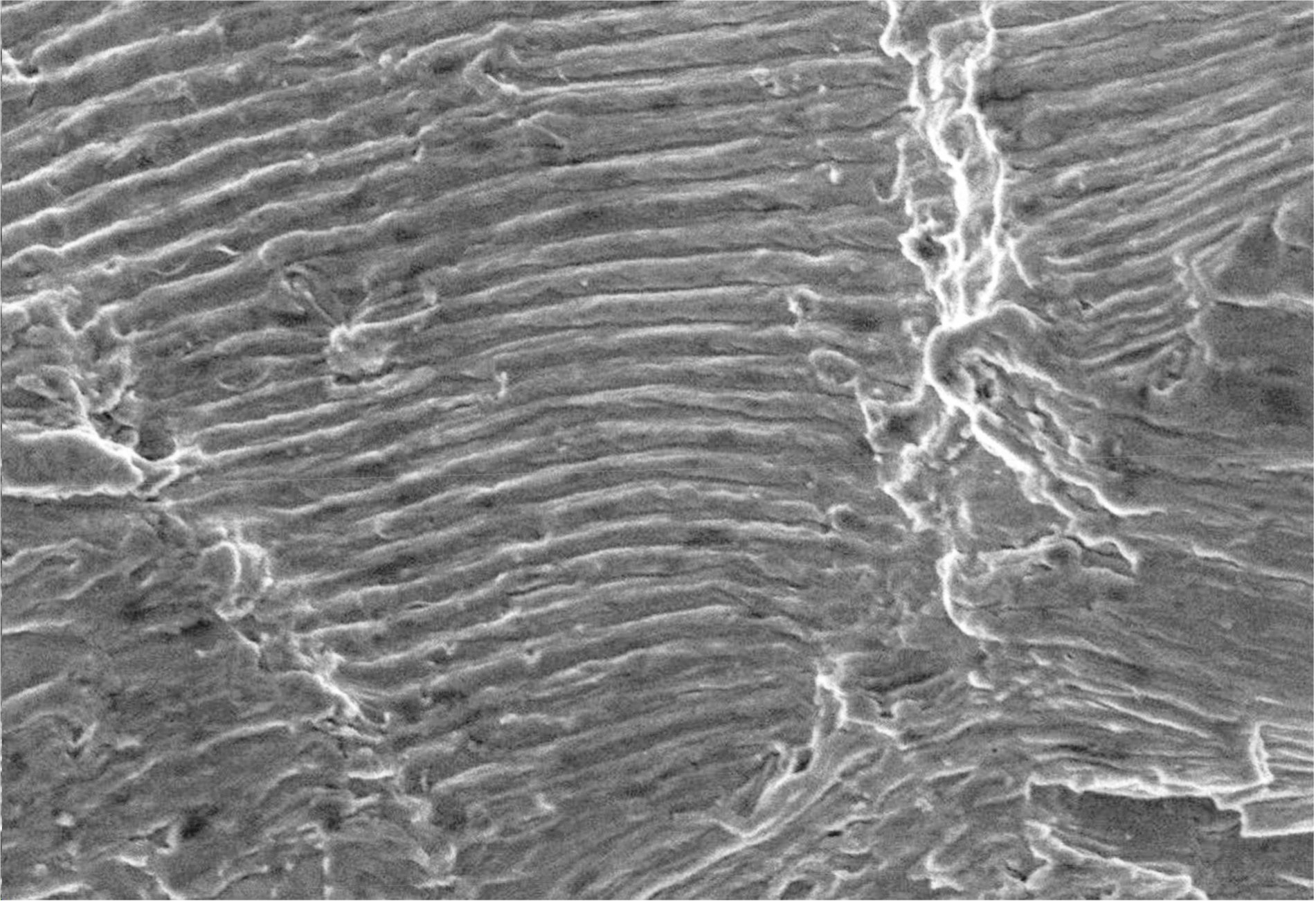
(c) 疲労破壊の破断面(ストライエーション状模様と呼ばれる縞模様が形成される)
図5 走査型電子顕微鏡による破断面の観察結果一例
(機械システム安全研究グループ 研究員 山口篤志)