機械システム安全研究グループの研究業務の紹介
1.はじめに
機械システム安全研究グループでは、機械・設備に起因する労働災害の防止を目的として、機械等の構造部材の強度評価、電子顕微鏡を用いた破面解析による機械の損傷原因の解明、機械を対象とした安全制御技術の開発、ロボットや介護支援機器などの人間機械協調型作業システムの開発などの研究を行っています。また、クレーンや建設機械の破損事故などの災害調査、プレス機械や食品機械などの災害多発機械を対象とした行政からの要請を受けた研究などを実施しています。
以上の研究業務、災害調査業務、及び行政要請業務を3本柱とし、これらの相乗効果による業務の質の向上を図り、働く人の安全確保と安全技術の高度化を目指しています。
以下、機械システム安全研究グループが実施した主要な研究業務を紹介します。
2.ワイヤロープの経年損傷評価と廃棄基準の見直しに関する研究
製造業や建設業の現場では、経年劣化したワイヤロープの切断による労働災害が多発しています。このような災害を防止するために、クレーン等安全規則ではその日の作業を開始する前にワイヤロープの異常の有無について点検を行うとともに、次のような不適格なワイヤロープの使用を禁止しています。
- ワイヤロープ「一より」の間において素線の数の10パーセント以上の素線が断線しているもの
- 直径の減少が公称径の7パーセントをこえるもの
- キンクしたもの
- 著しい形くずれ又は腐食があるもの
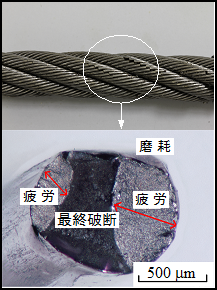
写真1 鋼製ワイヤロープの損傷評価
また、この研究では、新素材である炭素繊維ロープに対しても引張疲労試験を行い、疲労強度を明らかにするとともに損傷メカニズムの解明を試みました。この炭素繊維ロープの特徴は、切断直前まで劣化の兆候がないことが挙げられます。写真2に、炭素繊維ロープの劣化試験の状況を示します。
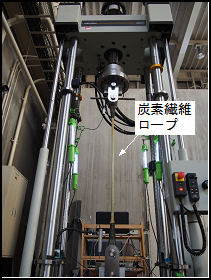
写真2 炭素繊維ロープの劣化試験
3.第三次産業で使用される機械設備の安全技術に関する研究
これまで、第三次産業で発生する機械災害の実態は、ほとんど解明されていませんでした。そこで、死亡災害と休業4日以上の災害を対象に分析を実施し、設備対策に重点を置いた労働災害防止対策の解明を試みました。その結果、死亡災害は廃棄物処理機械と昇降・搬送用機械で多発しており、これらの機械に重点を置いた安全技術の開発が重要と判明しました。
このうち、廃棄物処理機械に対しては、作業空間が広大で死角が多いという点に着目し、RFID(電波を使用した人や物の検出装置)、画像処理、レーザーなどを利用して作業者の存在確認などを行う支援的保護システムを開発しました。また、昇降・搬送用機械に対しては、フォークリフトを対象に、車体に設置された親機と作業者が保持する子機の間の無線通信を利用して周辺作業者が車体に接近するのを警告する運転支援システムなどを開発しました。
写真3に、作業空間が広大な機械を対象とした入退出ゲートと作業者識別用のRFID装置を示します。図1は、本研究で試作したフォークリフトを対象とした無線式運転支援システムの基本構成図です。
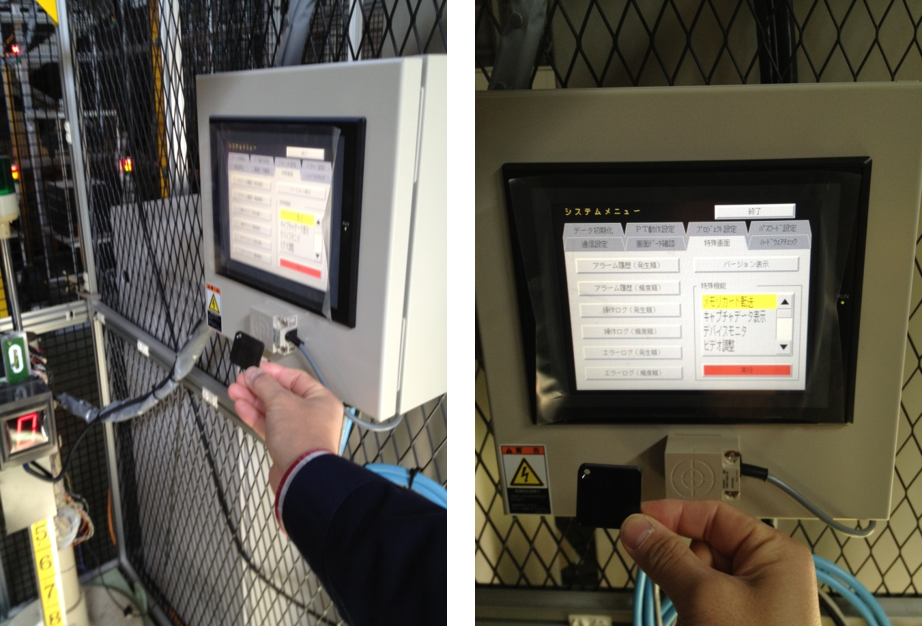
写真3 入退出ゲートと作業者識別用のRFID装置
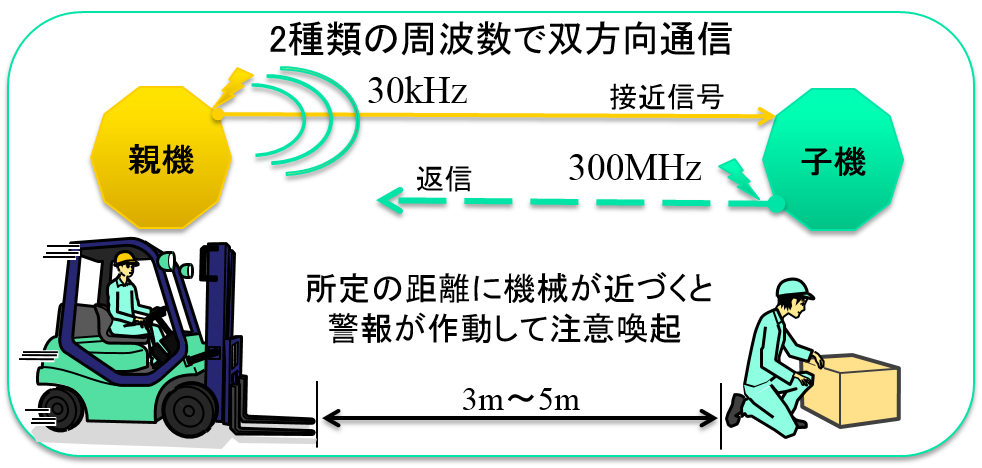
図1 試作した無線式安全運転支援システムの基本構成
4.災害多発機械の災害分析と防止対策に関する研究
機械に起因する労働災害は、年間約28,000件と全災害の1/4近くを占めています。そこで、災害多発機械であるプレス機械、食品機械、コンベヤ、粉砕機及び混合機などを対象に、災害データを分析して根本原因の究明と防止対策の明確化を図り、労働安全関係法令の改正などに活用するために研究を進めています。
このうち、プレス機械に対しては労働災害912件の詳細分析などを行いました。その結果、作業者が金型に特に近接するプレスブレーキ(金属板の折り曲げ機)では有効な対策がなく、レーザー式安全装置を利用した設備対策が不可欠であることなどを提案しました。また、食品機械に対しては労働災害1,487件の詳細分析などを行いました。その結果、食品機械に起因する災害は食料品製造業だけでなく小売業や飲食店などのサービス業でも災害が多いことや、スライサーやミキサーなどで圧倒的にリスクが高いことなどが判明し、サービス業でも実施できる安価な設備対策を提案しました。
写真4に、当研究所で実施したプレスブレーキ用安全装置の実証試験の状況を示します。写真5は、当研究所で実施したミキサー用安全装置の実証試験の状況です。
以上の結果は、動力プレス機械関係の労働安全衛生規則や構造規格の改正、食品加工用機械を対象とした労働安全衛生規則の改正などに反映されています。
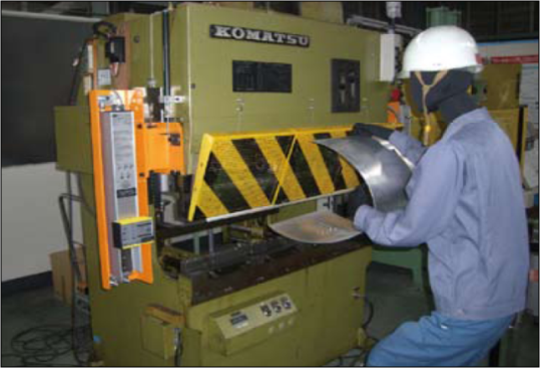
写真4 プレスブレーキ用安全装置の実証試験
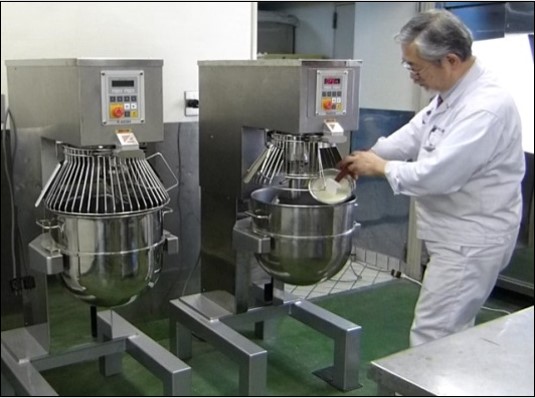
写真5 ミキサー用安全装置の実証試験
(機械システム安全研究グループ部長 梅崎重夫)