破断面を調べてみよう
1:破断面って何?
「物(もの)」が破壊すると、そこには必ず新しい「面」ができます。その面を「破断面」と言います。破断面には物が破壊した時の様子が残っていますから、これを調べれば逆に「どのようにして破壊したか?」がわかるわけです。当研究所の業務のひとつに災害調査があります。機械が壊れて労働災害が発生した時は、この破断面を調べることで事故の原因を突き止めたり、どのようにすれば事故を防止できるのか(再発防止)ということを提案したりします。
2:目で見てわかる破断面の特徴
破断面には様々な模様があります。そしてそれらの特徴は壊れ方(破壊機構)に対応していますので、模様の特徴を観察して見つけることが破断面の調査の第一歩となります。ここでは金属、特に鋼やアルミ合金などに見られる破断面の特徴について述べます。
破壊機構にはいろいろありますが、ここでは金属疲労について述べたいと思います。
金属疲労は繰り返し何度も力を受けた場所に亀裂(きれつ)ができて、その亀裂がだんだん長くなる現象です。同じ力を繰り返し受けた場合、最初は亀裂の伸びるスピードはあまり早くありませんが、亀裂が長くなると徐々にスピードは増して、最後は一気に破壊してしまいます。
図1は実験で作った金属疲労の破断面の一例です。何か模様とか、特徴を見つけることができますでしょうか?
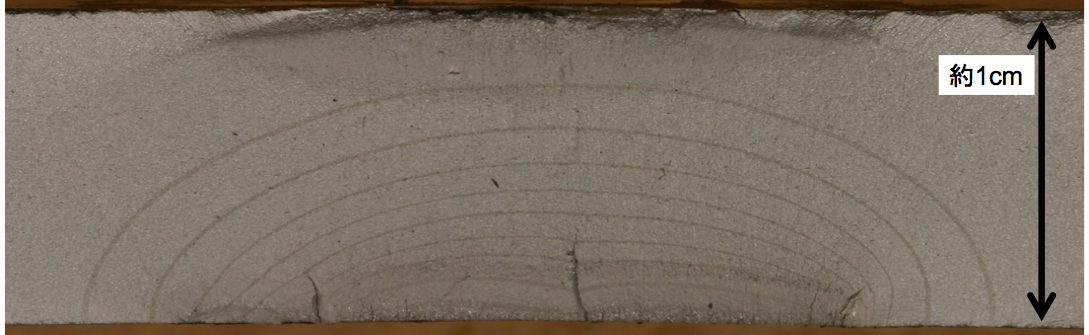
図1 疲労破断面の様子
一目見て気づくのは、レコード盤のような円弧状のスジ模様です。これは金属疲労の破断面にできるビーチマーク(波打ち際の波紋のようなマーク/貝殻模様とも言います)と呼ばれる模様です。亀裂が長くなる途中で、先端がここにあった証拠となります。ビーチマークは例えば機械が定期検査で停まっていた、あるいは今までよりも運転速度を上げた(下げた)など、かかる力の大きさが変わった時にできます。
もう一つの特徴はビーチマークが小さくなる方、画像では下中央の方に縦方向のヒゲのようなスジ模様があります。これはラチェットマーク(もしくはステップ)と呼ばれる模様です。この模様は、金属疲労の亀裂はこのあたりから始まったことの証拠です。
ビーチマークとラチェットマークの情報を合わせると、この破断面は次のようなシナリオでできたことがわかります。
- 画面下側の中央のところに亀裂ができた
- 亀裂は画面下から上に向かって亀裂が大きくなった
- 画面上側が残っていて、最後に破壊した
3:電子顕微鏡で見る破断面の特徴
破断面を調べるときには電子顕微鏡は欠かせない装置の一つです。電子顕微鏡を使って破断面のミクロスケールの模様を見ると、それは目で見たときとは全く違う世界が広がっています。
例えば図1の破断面を電子顕微鏡で観察すると図2のような模様が観察されます。
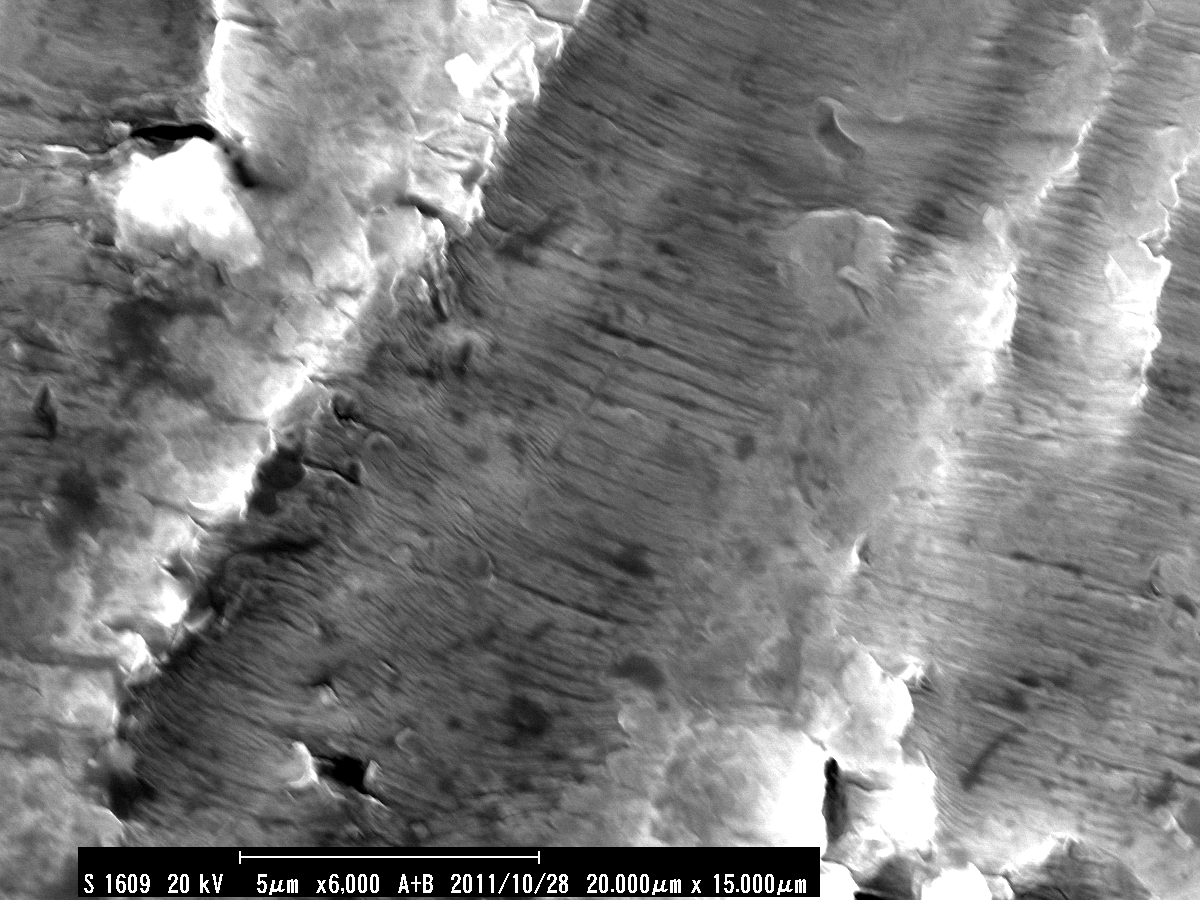
図2 疲労破断面を電子顕微鏡で見た時に観察されるストライエーション(縞模様)
画像の中にたくさんの小さな縞模様があることがお分かりいただけますでしょうか。こうしたミクロの模様は、金属疲労の破断面にしばしば観察されます。この模様はストライエーションと呼ばれています。もちろん目で見える模様ではなく、電子顕微鏡を使わなければ観察できません。この縞模様の幅は約0.3µm(3mmの1万分の1)です。
力が1回かかると1本のストライエーションができて、亀裂はストライエーションの幅だけ長くなります。つまり1万回の力がかかれば3mmだけ亀裂が長くなります。実際はもっと複雑な計算をしますが、例えば厚さが6mmの板の破断面に、このストライエーションが観察されたとしたら、破断するまでに力は2万回かかったということになります。
また、ストライエーションの幅はかかった力の大きさに関係があります。簡単な話として、幅が広いストライエーションがある場合には、大きな力の変化があった証拠となります。一方、幅の狭いストライエーションがある場合には、力の変化は小さかった証拠になります。そして、ストライエーションの幅(S)から、例えば計算式(注)、もしくは疲労亀裂進展曲線[2]と呼ばれるグラフを使って、かかっていた力と関係のある応力拡大係数(K)と呼ばれる値を求めることができます。さらに応力拡大係数と力の関係式は様々な文献に紹介されております[3]。こうして、破断面ができた時にかかっていた力が推定されます。
(注)ストライエーションと応力拡大係数の関係は、例えば次のような計算式[1]で示されております。ここでνはポアソン比、Eはヤング率です。
S = 9.4(1-ν2)(ΔK/E)2
4:再発防止に向けて
いかがでしたでしょうか。破断面には多くの種類があります。これを目で観察し、電子顕微鏡でミクロの世界を観察することで、事故になるまでの過程を明らかにすることができます。
どんなに堅固に作っても、いつかは必ず物は壊れます。そのようなときに、破断面を調査することで、なぜ壊れたのか?と言うことがわかるようになります。その次には必ず「どうしたら壊れなくなるのか?」という疑問が湧き、改善していくことでより壊れにくい、安全な製品ができ、そして安全な社会ができていくのだと思います。破断面の調査は、こうした活動の重要な要素であります。
破断面について相談をお受けする機会が多くありますが、最近、少し気になることがあります。色々とお持ちいただいた破断面や調査結果の書類など事故や損傷についての資料を使ってお話をした後に、お見えになった方が頭を掻きながら「資料の中身はよくわからないのだけど、大手の分析会社の結果だから大丈夫だろうと思っていました。」というケースです。調査結果がよくわからないので鵜呑みにする、または無条件に再発防止策として実行しようとしていることがあるようです。こうした場合、出てくる再発防止の結論には、どこか抜けやもう少し深められるのではないか?と思わせることや、場合によっては全くその機械のことを知らない会社が調査したため、結果として再発防止策にはなっていないというケースも見受けられます。
不十分な対策は、事故を防ぐどころか、さらなる事故の原因となります。今後とも、損傷と破壊に対して真摯な姿勢と地道な改善の積み重ねで、事故の原因を調べ、再発防止を考えていきたいと思います。
参考文献
- [1] 小林,材料科学,Vol. 17 (1981), p. 282
- [2] 日本材料学会,”金属材料疲労き裂進展抵抗データ集”
- [3] 日本材料学会,”Stress Intensity Factors Handbook”
(機械システム安全研究グループ 主任研究員 山際謙太)