貯槽内での作業前にしなくてはいけない換気
貯槽で事故が起きている
化学物質を扱う工場で、爆発・火災や中毒、酸欠事故がたびたび発生し、死傷者を生じたり、製造設備が破損したりしています。化学物質による事故というと、例えば、「製造プロセスに不具合があって、意図しない化学反応が起きて爆発しました」あるいは、「操作ミスや設備の故障などで化学物質が漏れ出て、火災や爆発が起きました」という事故がまず思い浮かぶと思います。確かにそのような事故が起きているのですが、死傷者が多い事故を調べてみますと、化学設備の維持保守作業中や設備の撤去や改修工事中(図1)であることが目に付くのです。
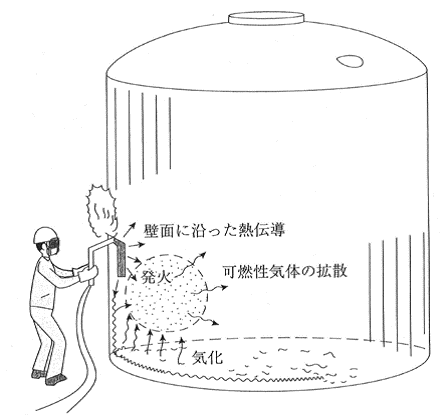
図1 ガス溶断中の貯槽内残留物の気化による爆発事故(八島研究員より提供)
その理由を調べてみますと、次のようなことがわかりました。化学物質を扱う工場内では、通常の稼働中、火気厳禁の場合がほとんどです。ところが、維持保守作業や改修工事では、通常稼働中には実施することがない、ガス溶断作業や切削工具による切断作業等が行われ、裸火を使用したり、火花を発生する工具や工法が使用されたりすることにより、爆発・火災の可能性が高くなります。そして、限られた期間で作業を完了するために、作業現場に複数の事業場からの多くの作業員が集中しがちです。その結果、事故件数が目立ち、また被災する作業員の人数も多くなりやすいのです。
どうして事故は起きるのだろう
通常時に火気厳禁のエリアで火気を使用する場合には、どのような目的で、どのような工具・工法を使い、どのような作業をするのかを火気管理者へ事前に申し出て、火気の使用許可を得ます。使用許可の条件のひとつに、「爆発・火災・中毒災害の原因となる物質を除去し、基準以下の濃度または量にしてから作業を開始すること」があることが普通です。
いま、原料を入れていた貯槽に腐食や破損がないかを検査することを考えてみます。最初に、入っていた原料を別の貯槽に移して中身を空にします。次に原料の性質に応じた洗浄剤を使って、残っている原料を洗い流します。その後、換気をして貯槽内を乾かしてから、酸素濃度とガス濃度を測定します。酸素が十分にあって、さらに、可燃性ガスや有毒ガスが無くなったことを確認できたら初めて、貯槽内に入って作業を始めることができるのです。
この貯槽内での作業中に事故が起きるのはなぜでしょうか。答えは簡単です。可燃性あるいは有毒性の物質が残っていたからですね。ではどうして残っていたのでしょうか。
理由の1番目は、換気の方法が適切ではなかったか換気量が足りなかった、あるいは、残留物からのガス発生などがあったにより、十分な換気がなされていなかった。2番目は、確認のためのガス濃度を測定していなかった、あるいは、測定をしていたが正しく測定されていなかった。この2つが重なった時に、中毒や酸欠事故が起きる可能性が生じます。さらに3番目として、ガス溶断作業での溶接火花のような着火源があったり、自然発火が起きたりすると、爆発・火災事故が起きる可能性が生じます。
事故防止のために換気をしよう
このような事故を防止するには、十分な換気をすることが一番です。しかし、そのために必要な換気量や換気時間は、初期の濃度や貯槽の容量・形状のほか、換気の流出入口の位置にも影響されます。そこで、小さな貯槽を使い、実際に換気を行って、ガス濃度の変化を測定してみました。すると、貯槽内のガス濃度は、一般住宅での室内換気とほぼ同じように変化していくことがわかりました。つまり、今後どのように貯槽内のガス濃度が変化していくかを推定することができて、ガス濃度がある濃度以下になるまでに、あと何時間換気を続ければ良いかの見込みが立つのです。
ただし、例えば、貯槽が複雑な形状であったり、内部に障壁があったりすれば、推定がうまくできません。とはいっても、うまくできないという意味は、理論的な推定式とは合わないということですから、今実際に計測した結果を推定式にフィードバックさせて新たに推定し直すことを繰り返せば、だんだん推定が実際の値に近付いていきます。
簡易計算図を使ってみよう
理論的な推定式は、数学の式としてはさほど難しい数式ではありませんが、四則計算用の電卓では、そう簡単には計算できません。そこで、計算機を使わなくても答えが出せる簡易計算図(図2)を作りました。この計算図では、貯槽の容積、換気装置の換気量、(実効)換気回数、換気時間、濃度倍率が図上で示されています。 使い方を説明しましょう。
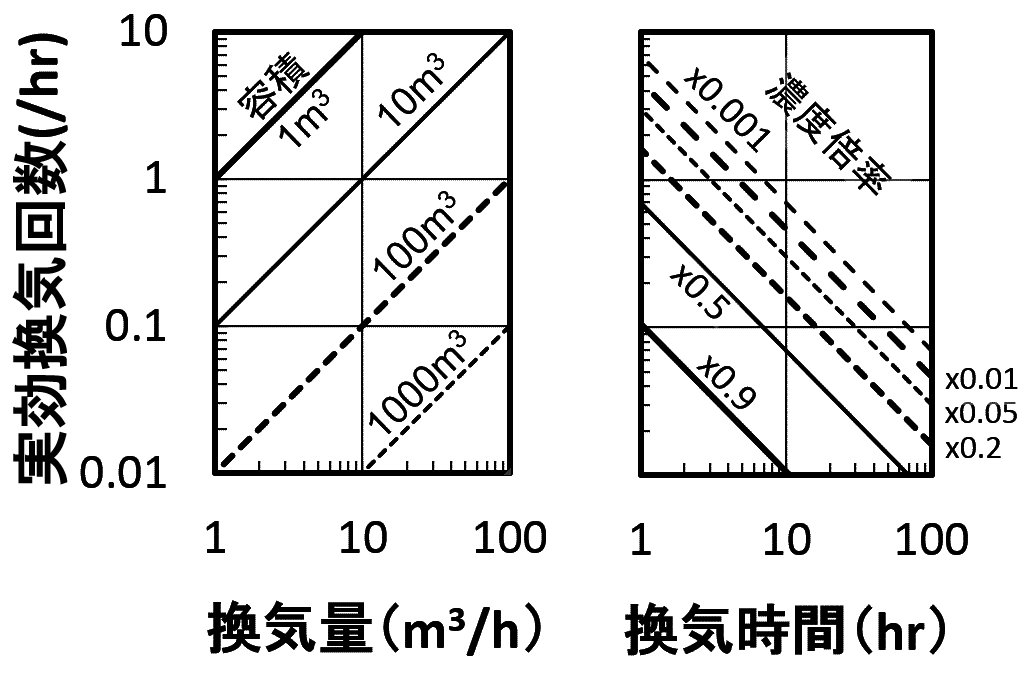
図2 簡易計算図
(1)貯槽の容積と換気量からの推算
作業計画を立てる時などで、貯槽の容積と換気装置の換気量が事前にわかっている場合には、①左図の換気量と容積の値の交点の位置から(理論上の)換気回数がわかります。②その交点から右図に水平に線を延ばします。③目標の濃度倍率値との交点から下方に線を降ろしますと、必要な換気時間が推算できます。逆をたどれば、ある換気時間で換気を終わらせたい時の換気装置の換気量を推算できます。
図3の例では、換気量が20立方m/h、容積が100立方mの場合、濃度倍率が0.2倍(濃度が初期濃度の1/5)になるには約8時間、濃度倍率が0.01倍になるには約22時間を要するとわかります。ただし、換気装置の換気量は、使用状況によっては仕様値よりも低下しますし、推定式どおりに換気が進むとは限らないので、現場での濃度測定が必要です。
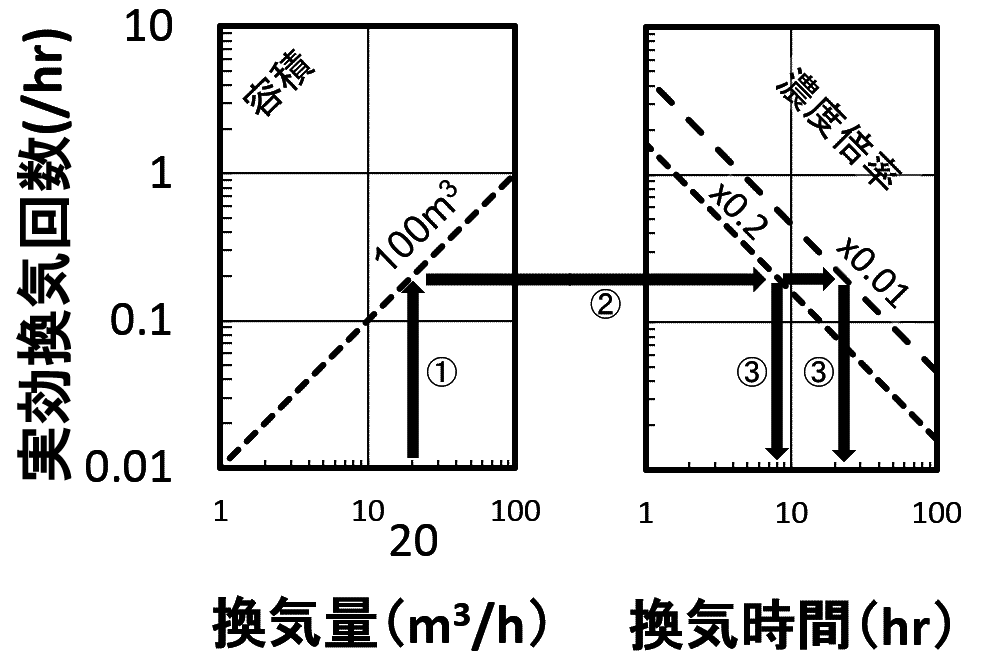
図3 貯槽の容積と換気量からの推算
(2)換気中の濃度計測値からの推算
貯槽の容積と換気装置の換気量が両方ともわからない時は、とりあえず何時間か換気を行ってみて、換気前と換気後の濃度の計測値から濃度倍率を求めます。すると、①換気時間と濃度倍率の交点から実効換気回数が定まります。②その交点から右へ水平に線を延ばします。③目標の濃度倍率との交点から下方に線を降ろしますと、必要な換気時間が推算できます。
図4の例では、2時間の換気をしたところ濃度が半分(濃度倍率が0.5倍)になりました。すると濃度倍率が0.01倍となるのは換気開始から約13時間後とわかります。つまり、濃度倍率を0.01倍とするには、さらに続けて約11時間の換気をすれば良いことになります。
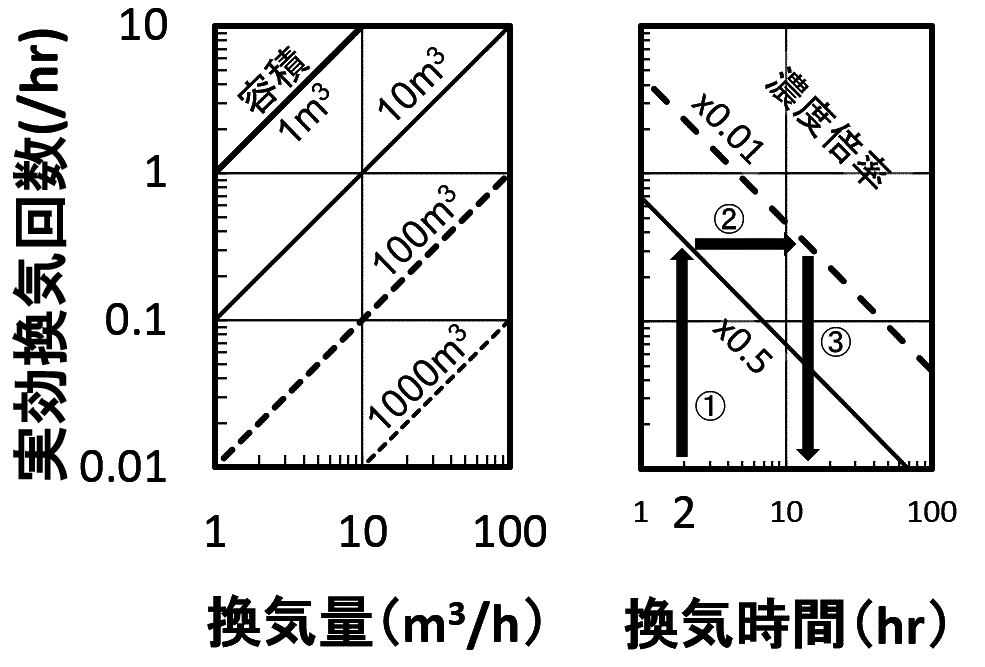
図4 換気中の濃度計測値からの推算
(3)使用上の注意
この簡易計算図は、理論的な推定式にガス濃度の変化を近似できるときにしか使用できません。したがって、貯槽の形状や流出入口の位置関係により使用できない場合もありますので、作業前に適正な測定方法で濃度を確認することを怠ってはいけません。その濃度の確認では、単に作業が許可される基準値より上か下かではなく、計測値の濃度変化が推算値の濃度変化と合っているかに注意することを奨めます。濃度変化の一致が確認できれば、推算値の信頼度が高いと期待できるからです。
このほか、換気中に残留している残査やスラッジなどからのガス発生がありますと、いくら長時間の換気をしても、理論的にある濃度以下には下がりません。すなわち、有毒ガスの時のような低濃度まで換気しなくてはならない場合には換気だけでは対処できませんので、エアラインマスクや防毒マスクといった保護具の使用など、別の手段を併用する必要があります。
換気を実施する際のポイント
(1)換気口の位置
換気口の位置は、入口から出口へのショートカット(近道)ができないように、貯槽内をできるだけ均等に流れるようにすることが要点です。具体的には、流入口と流出口をできるだけ離して、長い距離を流れるようにしたり、内部でよどみができそうなところの近くに流出入口を設置したりしましょう。
また、有毒ガスなどで低濃度のガスが対象であるならば、濃度差による拡散・混合よりも、温度差による拡散・混合の方が効率よく換気できますので、流出入口の高さの差を利用しましょう。
(2) 換気口が1つしかない場合
換気用の口が1箇所しか用意できない場合では、その流入口からパイプをできる限り奥まで差し入れることによって、擬似的に流出入口を2箇所にすることができます。
(3) 貯槽内濃度の測定方法
推算をどのように行うのであっても、最終的には貯槽内の濃度を測定し、作業を実施できる濃度であることを確認してから、作業を開始しなくてはなりません。したがって、その測定に不備があれば、不測の事態が起こらないとも限りません。
最も避けなくてはいけないのは、貯槽内の濃度を測定しているつもりで、知らぬ間に流れ込んでいた外気の濃度を測定してしまうことです。換気口付近では特にその可能性が高くなりますから、例えば、①計測用の採取パイプを差し入れたまま換気口をいったん閉めて計測する。②採取パイプをできるだけ奥まで差し入れ、その採取パイプの長さに見合うだけ待ってから計測する。③換気口から離れた箇所の別の小穴を使用して計測する。といった方法があります。
このほか、基本的事項として、ガス濃度計は対象とするガス種が決められていること、日常のメインテナンスや校正が適切に行われ、計測誤差が本来の仕様を満たしていることが必要です。